A pre-condenser is a type of heat exchanger that is used to partially condense the inlet process stream. Pre-condensers are always a considerable option when a significant amount of the process stream is condensable. A vacuum system that incorporates a pre-condenser will decrease the size of the pump required; thus, the total energy requirements and capital costs will be lower.
Types of heat exchangers used in process vacuum systems
- Pre-condenser: A vacuum condenser placed after a knock-out pot but before the front of a pump
- Sealant heat exchanger: Use a heat exchanger in full recovery systems to cool the sealant liquid before recirculating it back into the pump
- Inter-stage heat exchanger: A condenser placed between two pumps or a booster and a pump to cool the process stream
- After-condenser: A condenser placed after the pump

Inter-stage heat exchanger
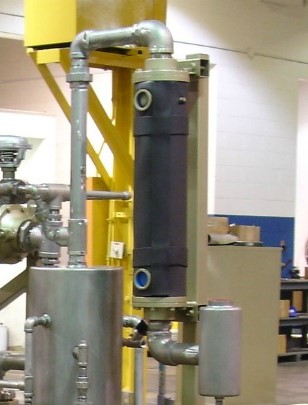


Why Wintek?
For 30+ years, Wintek has been using condensers in strategic positions to optimize the results of process vacuum systems. For example, pre-condensers placed in front of a pump, compacts the gas into a liquid before it enters the vacuum pump. This saves the end user time and resources by reducing the size of the vacuum pump.
Our engineers consider pressure drop, behavior of condensate, amount of non condensable gases, endothermic and exothermic chemical reactions, vapor pressure, equipment layout, and other factors when sizing the correct vacuum condensers for your processes. In addition to these process parameters, it also takes the cooling liquid and size of the system into account. For example, in larger systems, many companies use one big condenser; however, in some of these cases Wintek recommends two smaller condensers. The first condenser uses tower water to lower the temperature of the process stream. Then the second condenser uses chilled water to cool down the rest of the process stream. With this configuration the user can save money by using less chilled water than would be used with a single larger condenser.